Integrated Solutions
to Modernize Your Plant
Bulk Material Handling Equipment and Systems
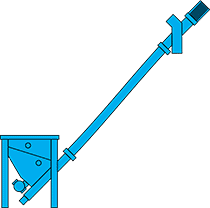
Flexible Screw Conveyors
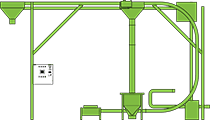
Cablevey Conveyors
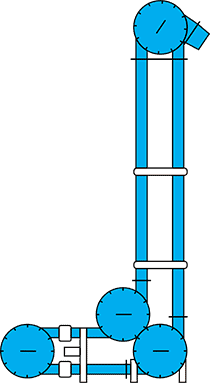
Aero Mechanical Conveyors
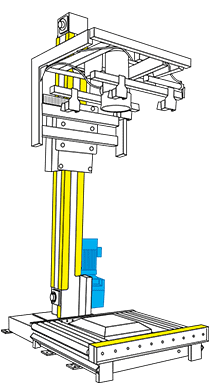
Bulk Bag Fillers
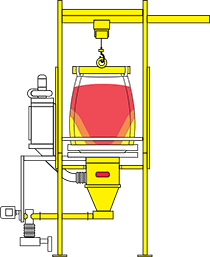
Bulk Bag Unloaders
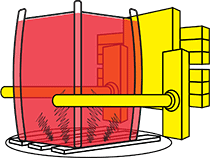
Bulk Bag Conditioners
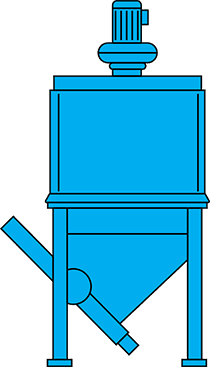
Bag Dump Stations
Our Company
Spiroflow is a global leader in the field of powder handling and dry solids processing and an emerging leader in control systems integration. Throughout our 45-year history, our design engineers and process automation team have provided customers with the safest, most efficient, innovative and most reliable process solutions available.
Yes, we were an early inventor of the flexible screw conveyor, but we’ve grown significantly since those early days as have our products and service offerings. Spiroflow delivers engineered solutions designed to solve your greatest handling and processing challenges, whether it is a single conveyor or a complete powder handling system with integrated controls.
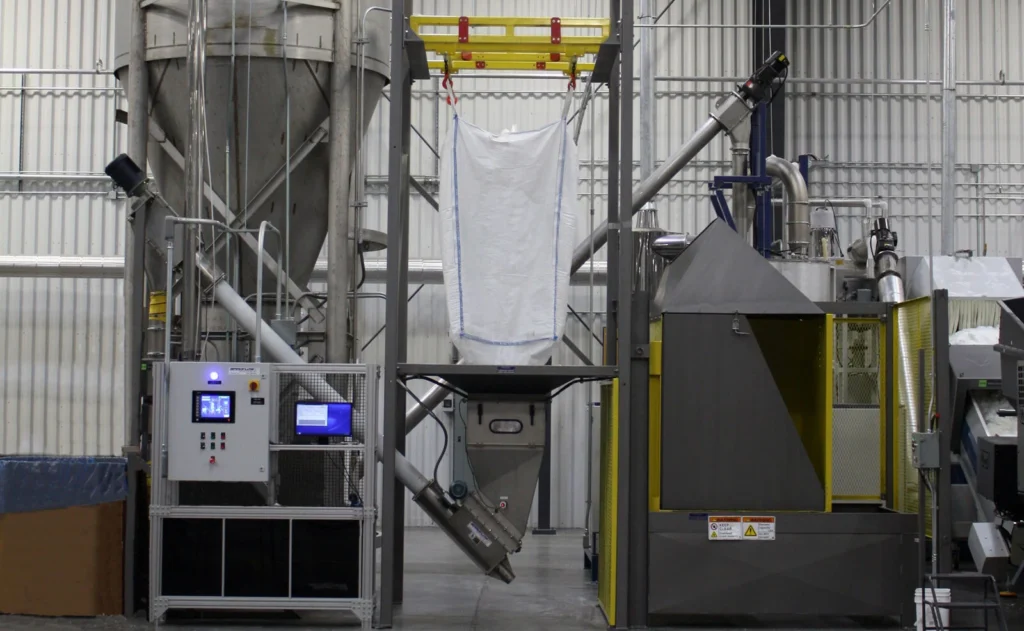
SPIROFLOW SOLUTIONS
Empowering Industries, Raising Productivity
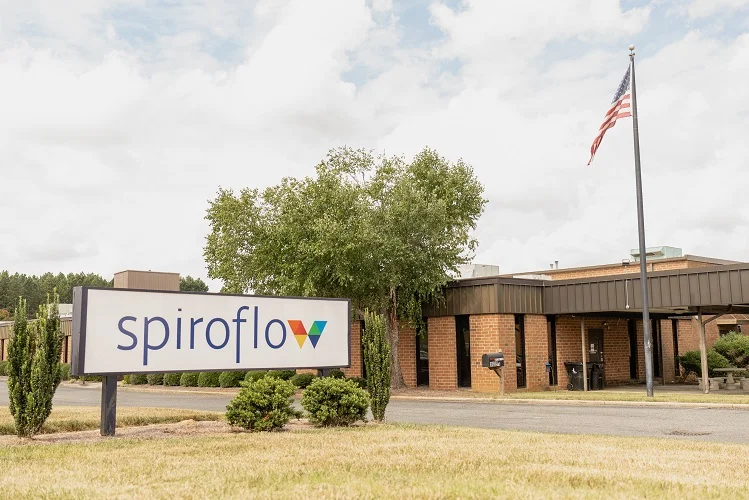
Spiroflow offers a wide range of conveying solutions, bulk bag fillers & unloaders, and additional equipment needed for automated bulk handling of materials.
Our comprehensive product range includes solutions for the most advanced conveying, weighing, filling and discharging applications to meet the growing demands of processors. By definition, we understand that most processors need more than a single piece of equipment. Spiroflow engineers have decades of experience putting all the components together and seamlessly integrating them into your existing plant.
At Spiroflow, we believe that after-sales support and service form an integral part of every bulk material handling solution that we provide. We have systems that have been in operation for decades and that means that they are not only well made but well maintained.
We have a database of product conveying trials logged over thirty years, taking the guesswork out of assessing flow rates and expected performance. If you are not able to witness a trial, we can send you a video with a full test report and recommendations.
Brands We Keep Moving
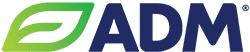

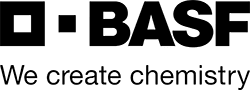
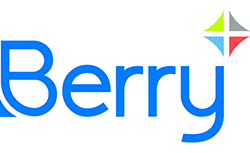

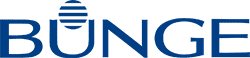
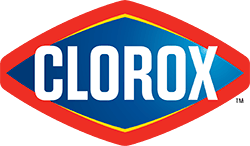
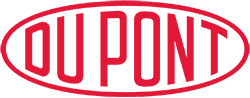
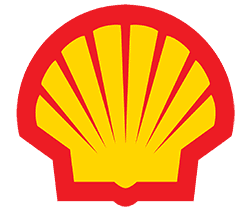
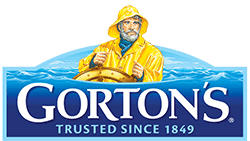
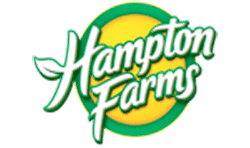
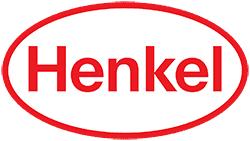
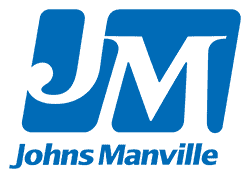
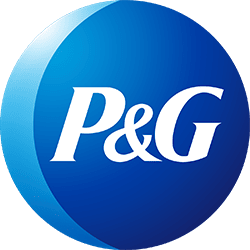
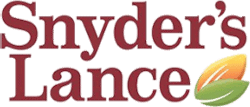
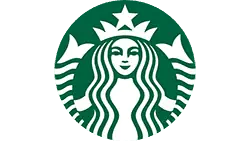
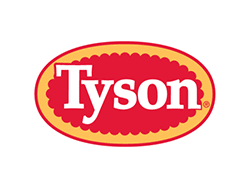
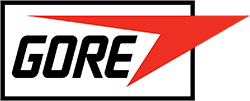

Spiroflow Automation
Spiroflow Automation is a full-service industrial control, networking and automation provider. We specialize in control system integration; specifically, PLC and motion control, press control and process automation. From stand-alone machines to multi-controller plant-wide systems, Spiroflow pairs a depth of engineering expertise with creative technological solutions to help our customers increase production, reduce costs and improve safety.
Resource Hub
Company Reg: 01210198 VAT Reg: GB 732 911 249
- Privacy/Cookies Policy
- Terms & Conditions
- Terms & Conditions of Sale
- Conditions of Purchase
- Copyright 2024 Spiroflow. All Rights Reserved.
- Developed by: MBI